The Tx51 tempers are subjected to a mechanical stress relief that can be thought of as stress aligning. The residual stresses in heat-treated 7075 aluminium alloy blocks have been characterised using two neutron diffraction strain scanning instruments.
7075 Aluminum Get To Know Its Properties And Uses Gabrian
Aluminum alloy 7075 in particular has one of the highest attainable strength levels of all forged alloys and is capable of good stress corrosion resistance.
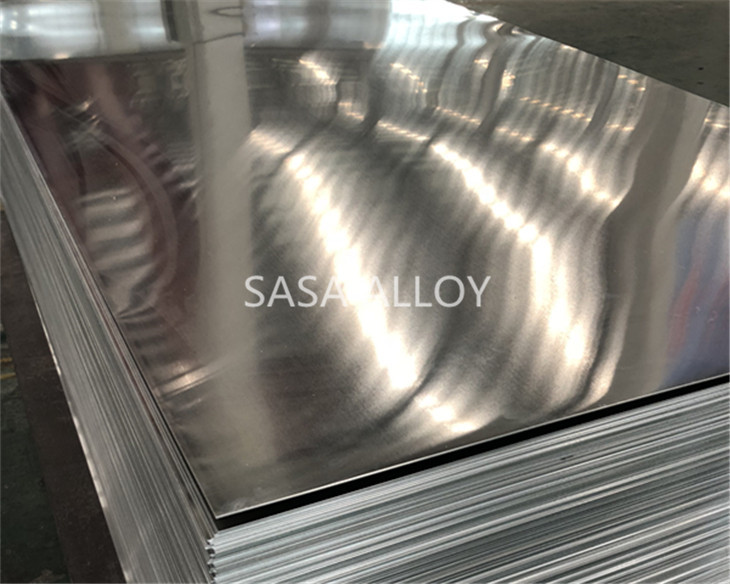
Stress relief 7075 aluminum. Furnace-aged at a temperature above room temperature aluminum alloy. For these reasons aerospace engineers have historically preferred to specify 7075 aluminum forgings in the T73 temper for components used in helicopters airplanes and ordnance. Stress relief procedure for Al 7075-T6 swall Materials 27 Mar 07 1343 I have observed a reduction in residual stresses by changing from a T6 condition to a T7 as suggested by CoryPad although it was on a 355 casting not a 7075 part.
The stress relief is accomplished by stretching the metal by an amount that depends on the type of standard wrought product being made sheet plate bar or forging. Materials Science and Technology. I have a problem that I am seeking a solution for.
I am machining a very large plate of 7075-T6. Aircraft fittings gears and shafts fuse parts meter shafts and gears missile parts regulating valve parts worm gears keys aircraft. 7075-T651 aluminum is 7075 aluminum in the T651 temper.
Very high strength material used for highly stressed structural parts. This will relieve the stress that occurred during the work hardening process and help resolve warping and other issues. 2 7075 aluminium alloys composition roughly includes 5661 zinc 2125 magnesium 1216 copper and less than a half percent of silicon iron manganese titanium.
It is one of the most commonly used aluminium alloys for highly stressed structural applications and has been extensively used in aircraft structural parts. The aluminum is heated to temperatures between 570F and 770F for up to three hours. It has numerous large pockets and large through holes with wall thicknesses from 125 to 187.
The T7351 temper offers improved stress-corrosion cracking resistance. 108 rows General 7075 characteristics and uses from Alcoa. The post-cold-work residual stress right is significantly reduced.
Vibratory stress relief is a green and efficient aging technology compared with traditional natural stress relief and thermal stress relief. One of the benefits of annealing is it can be used on alloys that are considered non-heat treatable such as those in the 3xxx 4xxx and. 54 long x 18 wide x 15 thick.
The degree of overaging is chosen so as to maximize stress corrosion resistance. The reduced residual stress level in the stress-relieved state has significant advantages in terms of ease of machining reduced distortion and improved part performance. The material was recieved with a slight 080 bow.
Residual stress relief in the aluminium alloy 7075. Increasing the magnitude of cold compression from 1 to 10 has been shown to have a beneficial effect on the residual stress distribution by. Effect of vibratory stress relief on fatigue life of aluminum alloy 7075-T651 Jing Song and Yidu Zhang Abstract Vibratory stress relief is a green and efficient aging technology compared with traditional natural stress relief and thermal stress relief.
Figure 8 shows a hub assembly manufactured from 7075 aluminum bar. The research aimed to determine whether vibratory stress relief is feasible to improve the fatigue life of aluminum alloy 7075-T651 or not. C for 2 12 h is used to study stress relaxation over the entire stress strain curve at room temperature.
The post-quench residual stress left reaches as high as 200 ksi in this aluminum 7075 simulation. To achieve this temper the metal is solution heat-treated stress relieved then artificially aged. However its use is very popular in a variety of other industries due to its well-balanced set of properties.
The 7075-T6 aluminium is the preferred choice for the aerospace marine and transportation industries where low weight and high stress resistance are crucial factors. It is observed that the phenomenon of stress relaxation is accompanied by some hardening process the latter being dominant over the former at rather low tensile strains. The customer requires that the parts be heat treated to the T73 temper and requires residual stress levels be kept to about 6000 psi or below.
Aluminum 7075 alloy annealed at 413 C for 2 12 h is used to study stress relaxation over the entire stress strain curve at room temperature. Stress Relieving Heat Treated Aluminum Alloys. The influence of uniaxial cold compression 1-10 on relieving the residual stress has been determined.
To facilitate the machining operation the material is procured in the T7351. 7075-T6 is a very high strength solution treated and artificially aged ie. Aluminum 7075 alloy annealed at 413.
7075-T73510 aluminum is 7075 aluminum in the T73510 temper. It is observed that the phenomenon of stress relaxation is accompanied by some hardening process the latter being dominant over the former at rather low tensile strainsThe intrinsic height of the energy barrier to the movement of relaxing dislocation. Systematically increasing the magnitude of cold compression from 1 to 10 has been shown to have a.
The stress relief is accomplished by stretching the metal by an amount that depends on the type of standard wrought product being made sheet plate bar or forging. Stress relievingflattening 7075-T6 Plate. Kenneth Aerospace 6 Aug 01 1129.
The influence of uniaxial cold compression on relieving the residual stress has been determined. The residual stresses in heat treated 7075 aluminium alloy blocks have been characterised using two neutron diffraction strain scanning instruments.
7075 Aluminium Sheet Sasa Alloy Co Ltd
7075 Aluminium Sheet Sasa Alloy Co Ltd
Chemical Composition Of 7075 Aluminium Alloy Download Table
7075 Aluminum Get To Know Its Properties And Uses Gabrian
7075 Aluminium Tube Sasa Alloy Co Ltd
7075 Aluminium Sheet Sasa Alloy Co Ltd
0 Comments